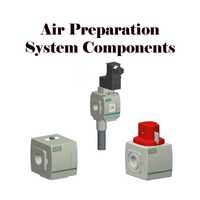
Item # OVERVIEW OF AIR PREP COMPONENTS
BRIEF OVERVIEW OF AIR PREP COMPONENTS
- UM : EA
Overview of Air Preparation Components
In any pneumatics system, ‘dirty’ air can be the cause of failed equipment. Air Preparation Systems keep air supplies clean enough to maintain effective functioning of pneumatic components.
Drip Legs are often the first line of defense. Changes in pressure can cause water vapor in ambient air to condense when compressed into the storage tank. Water vapor entering valves and cylinders can cause corrosion and sticking spools and rods. Drip legs use the condensation of air entering a chamber larger than the supply pipe to remove water from heavily contaminated air supplies. Drip legs are only effective against water but protect downstream filters from being overwhelmed by quantities of water that would degrade their capacity.
Particulate filters remove larger particles that contaminate air supplies. A 40 micron particulate filter (a ‘coarse’ filter) removes particles as small as one-and-a-half thousandths of an inch, with a 5 micron ‘fine’ particulate filter removing contaminants as small as two ten-thousandths of an inch. These particles cause wear on spools and valve seats and build-up on cylinder seals. Particulate filters also remove contaminants like rust and dust caused by air drying systems. Systems with steel pipe or air intakes in dusty environments benefit from particulate filtration. Particulate filter elements have a pleated design to maximize filter surface area.
Coalescing filters pass air contaminated with oil or water vapor through progressively coarser media to bring liquids together into droplets to be drained out of the filter bowl. Quality coalescing filters use a random matrix of glass fibers and epoxy resin to remove contaminants as small as .01 micron from air used for paint, electronics assembly, and robotics. Coarse coalescing filters (.3 micron) are incorporated into the air preparation chain as an initial protection against vapors and small contaminants, fine coalescing filters (.01 micron) are suited to point-of-use applications where air cleaner than the main supply might be needed.
Adsorbing filters remove the smallest contaminants such as fumes, vapors, odors, and ultra-fine dusts from an air supply, passing air over an activated carbon element to which contaminants adhere on a molecular level. Adsorbing filters are sometimes combined with coalescing filters into one unit and are often used immediately after a coalescing filter at the point-of-use. Adsorbing filters are used where air must be of high purity in applications such as pharmaceutical, food and beverage, and semiconductor assembly.
Regulators use a diaphragm or piston mounted between a spring and a valve stem to maintain a desired pressure in a pneumatic system less than the pressure supplied by the compressor. By balancing air pressure in a chamber below the piston or diaphragm with force supplied through the spring by an adjustment knob to the top of the piston, a valve is operated that allows air into the chamber until pressure there is enough to counteract the spring, closing the valve. As air is exhausted by tool use or valve exhaust ports, pressure in the control chamber is reduced to open the valve and rebuild the desired line pressure. Regulated air lets tools, valves, and actuators operate at pressures giving optimal performance. Non-relieving regulators hold pressure on the downstream side of the regulator. This has two benefits, acting as a check valve to hold cylinders or actuators in their activated position and preventing exhausted air from contaminating clean environments. Relieving regulators release downstream pressure that exceeds the regulator setting by means of a relief orifice in the control chamber. Relieving regulators eliminate the need for a separate relief valve in systems where back pressure may damage equipment. Regulators may be installed at the beginning of an air system, to maintain overall system pressure, at point-of-use to ensure correct function of components that require air pressures different than the main supply, or in both locations so that a wide range of applications may be used in a single system.
Lubricators add oil particles into an air supply to lubricate air tools such as ratchet and impact wrenches, drills, and grinders. By using internal chambers designed to create a venturi, oil is drawn from a reservoir and distributed as an aerosol to downstream air. Quality lubricators allow refilling the reservoir while the system is pressurized and may include electronic sensors to monitor oil levels and prevent tools from running without lubrication. Lubricators are often installed at point-of-use to keep the main air supply contaminant free for applications that do not require lubrication.
Diverter blocks provide four ports of additional sources of air at any point in an air preparation system. These can be used for applications that require different filtration, lubrication or pressures than the main air supply and can supply pilot air for valves and regulators. Diverter block ports can also house gauges, sensors, and pressure switches.
Shut-off valves are typically the first item in an air preparation system, using a manually operated ball valve to prevent air from reaching downstream equipment. This allows maintenance to be performed without shutting down the main air supply. Shut-offs often have an exhaust port to relieve downstream pressure when closed and may have a means to be locked closed during repair or maintenance of downstream components.
Slow start/Quick exhaust valves are often placed at the end of an air preparation system, they are usually an air pilot or solenoid valve that quickly releases downstream pressure when closed. When opened, quick exhaust/slow start valves slowly build up line pressure to prevent damage to downstream actuators.
Lock-out valves are most often seen at the end of an air preparation system. Unlike shut off valves, OSHA approved lock-outs must have a way to be padlocked in the closed position to isolate all downstream equipment from pressurized air. Lock-out valves also function as emergency shut-offs and are usually painted conspicuously. Some lock-out valves also feature a slow start function.
Mounting options for air preparation systems include panel nuts for smaller sized units, and metal brackets for larger sizes. Some manufacturers have combined quick-connect clamps between air preparation components with mounting brackets, allowing rapid replacement of individual components while also providing a secure mount for the air preparation system.
NOT FINDING WHAT YOU NEED?
SEND US AN E-MAIL:
SALES@THEPNEUMATICSTORE.COM
Specifications
ARTICLES REGUARDING | AUTOMATION COMPONENTS |